Our quality management
We aim to satisfy customers with both quality and cost under the slogan of “Product Innovation” (promoting technological innovation to improve productivity and quality).
Through mutual communication between our customers, our company, and our partner companies, we will work diligently and speedily to resolve quality issues faced by a wide range of products, from single items to mass-produced products.
Quality efforts
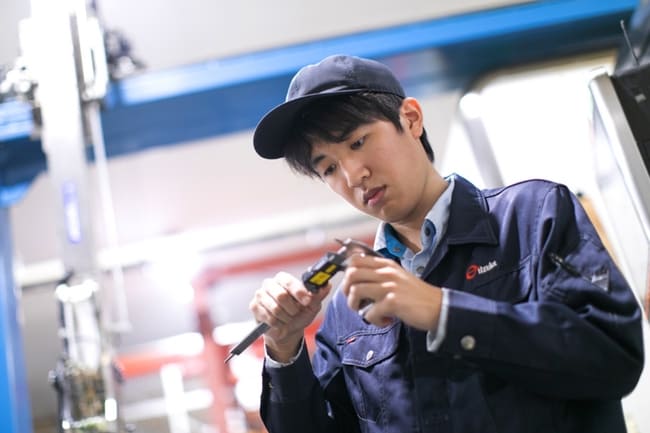
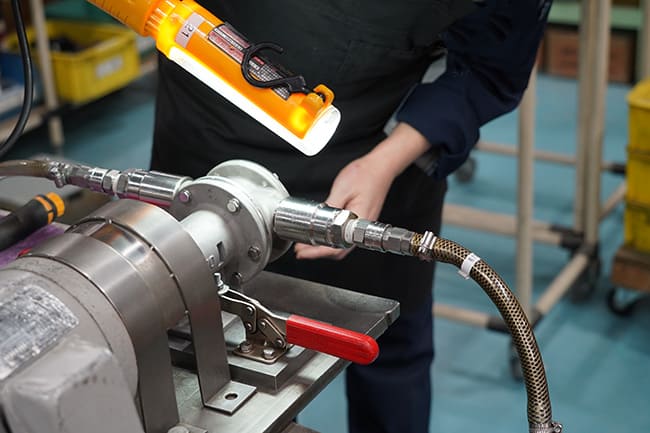
We committed to through quality control throughout the entire process, from incoming to outgoing inspections, based on the following five initiatives, and faces quality improvement on a daily basis to ensure stable production.
-
Clarification of procedures, accumulation of know-how
We are working to standardize work by enhancing “setup instructions” and “tool sheets” that contain information on programs and tools to be used.
Expertise gained through experience is reflected in these standards to share knowledge and realize accurate and speedy machining.
As a result, this has led to the development of young employees and the prevention of recurrence of nonconformities. -
Accuracy control during continuous robot operation
Continuous robot operation is an extremely important means of dramatically increasing production efficiency in mass-production machining, but its operation naturally entails risks.
We monitor dimensional data and manage it to maintain stable accuracy even when the robot is in operation. -
Recurrence of non conformities
We take customer complaints and internally discovered nonconformities as opportunities for improvement, and work diligently to prevent recurrence.
We identify the true causes through “why-why” analysis and take appropriate measures such as reviewing programs, jigs, and tools.
Even in cases where it is difficult to solve problems that originate from drawings or materials, we proactively make proposals for optimal QCD through communication with our customers. -
Inspection Strengthen & Feedback
We have been visualizing dimensional variations using histograms and control charts, and from2021 we are promoting the digitalization of the system and working to develop tools that will enable us to capture them more visually.
We are also trying to reduce the risk of defect occurrence by P-FMEA for some products, which is useful for quality control.
We aim to achieve a process control capability (CPK) of 1.33 as a target value for mass-produced products. -
Continued guidance to Cooperative companies in Overseas
In addition to notifications when nonconformities occur, we work to improve quality by sharing information through periodic web conferencing and providing proposals and guidance on specific countermeasures.
【Inspection】
01Receiving Inspections
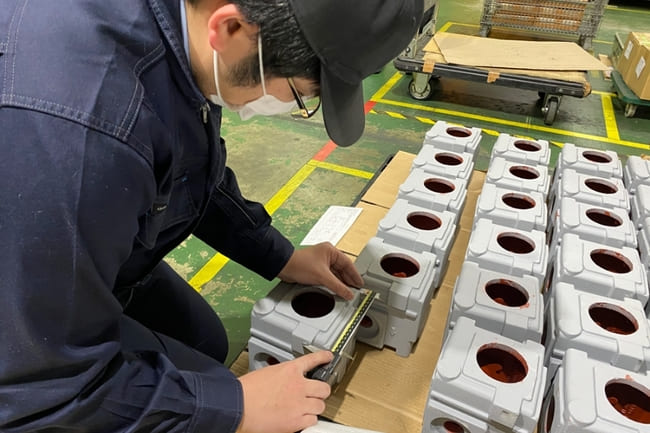
【Material:Casting material、Round bar、Steel Plate】
We inspect spot checks to ensure that the products are delivered according to the dimensions of the order.
Mainly dimension and appearance. Not only checking Mill sheet but also JIS G 5121 and other required specifications, and periodically conduct component analysis and microscopic observation of metallographic structures in corporation with external public institutions.
We also inspect materials supplied by customers and report any problems in advance, check passive film of stainless steel, and perform other inspections as requested.
【Processed products: Semi-processed and full processed at partner companies】
Based on the inspection report, we inspect dimensions and geometric tolerances by spot checking.
Inspection results are compiled as data and fed back to subcontractors as necessary to discuss improvement measures to improve accuracy.
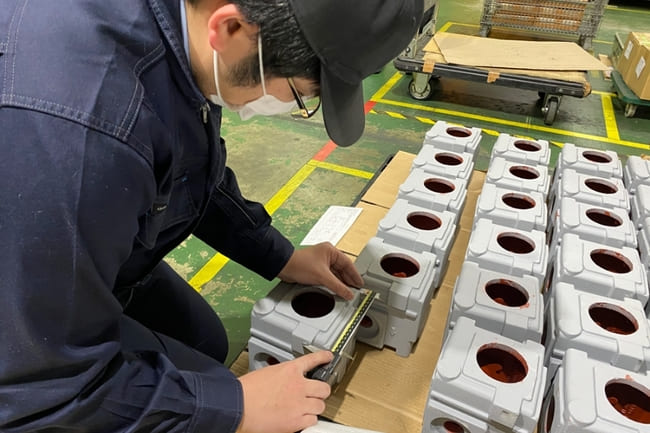
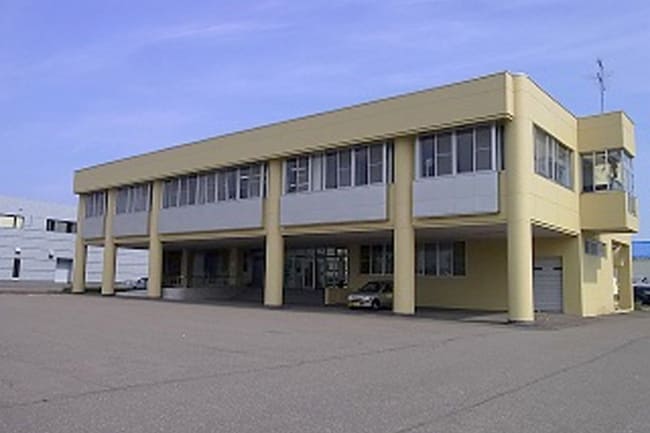
02Process Inspections
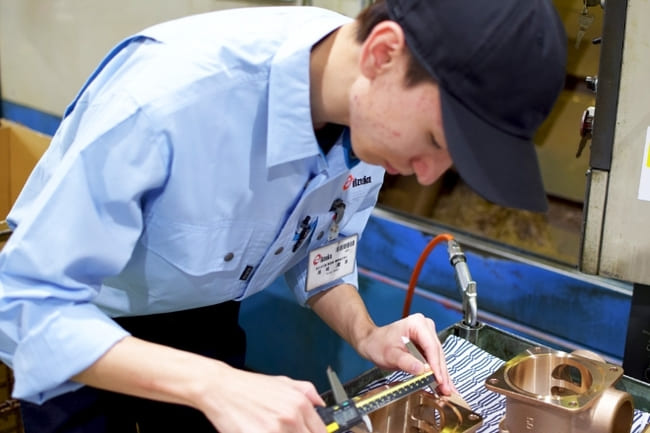
In process inspection
This inspection is performed by machine operators in the machining process.
Based on a pre-directed checklist, the machine operator checks whether the machine operator checks whether the machine has been processed according to the dimensions on the drawings.
the frequency is determined according to the number of pieces processed, such as the first piece.
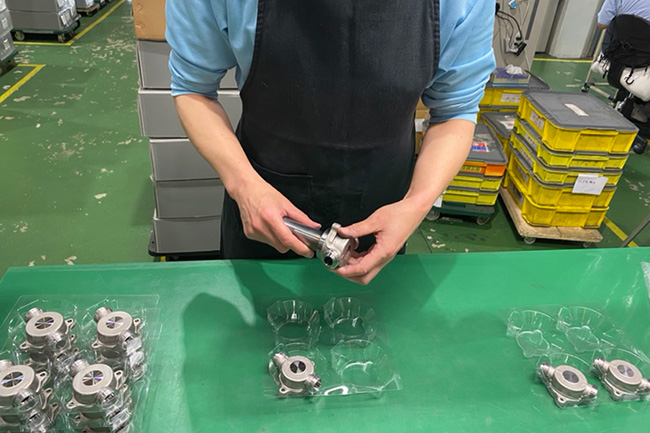
Inline Inspection
This inspection is performed by machine operators in the machining process.
Based on a pre-directed checklist, the machine operator checks whether the machine has been processed according to the dimensions on the drawings.
The frequency is determined according to the number of pieces processed, such as the first piece, morning noon, and evening.
Items that are difficult to measure in the process, such as geometric tolerances, are brought to the inspection room for checking.
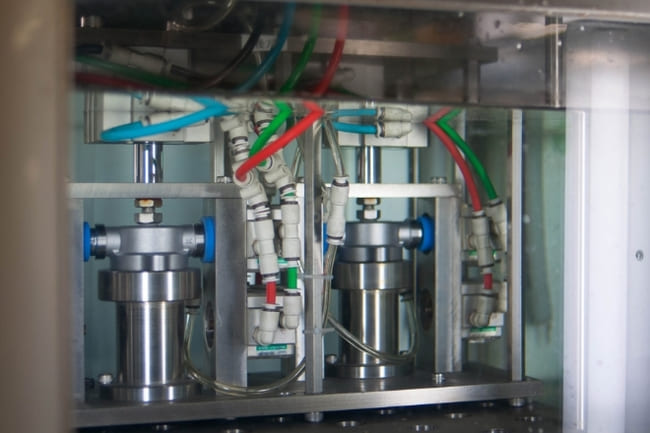
Leak Inspection
Even if the dimensions and surface roughness meet the drawings, problems may arise after the product has been incorporated into the customer’s product due to minute flaws or casting defects.
Some products are tested to check for defects and water leakage in submersion using a leak tester manufactured in-house.
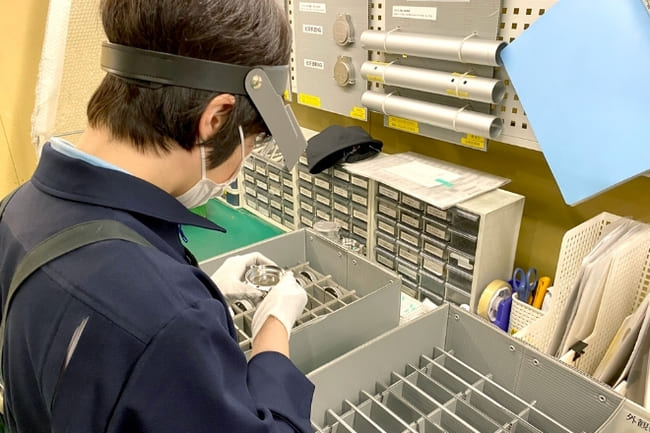
Dimensional Inspection
Over the past few years, we feel that our customers have become more demanding regarding “appearance”.
In order to meet the demand for appearance quality, we conduct visual inspections for flaws and dents in an illumination-controlled inspection booth.
In the semiconductor field, we also conduct total inspection using a microscope.
03Shipping Inspection
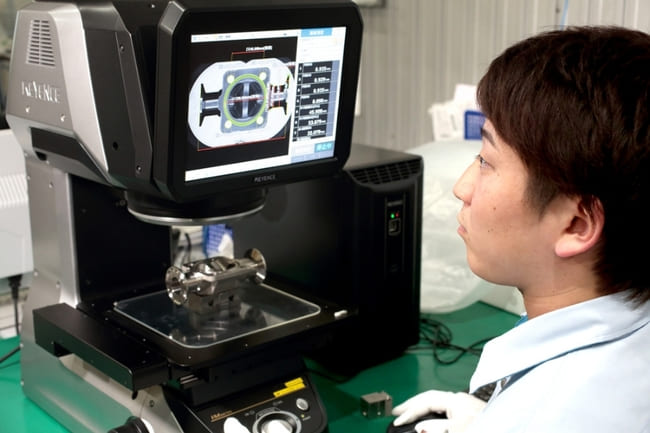
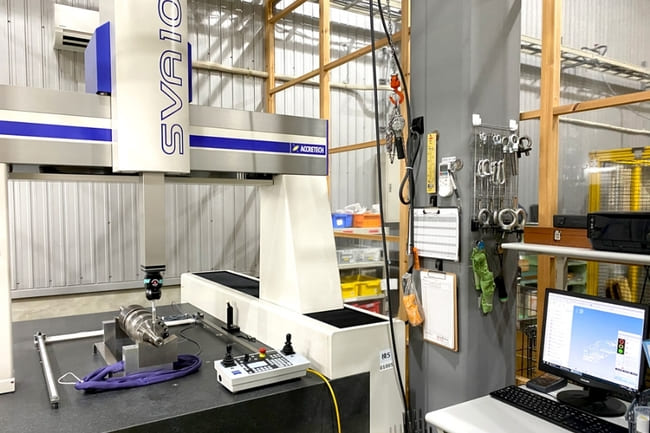
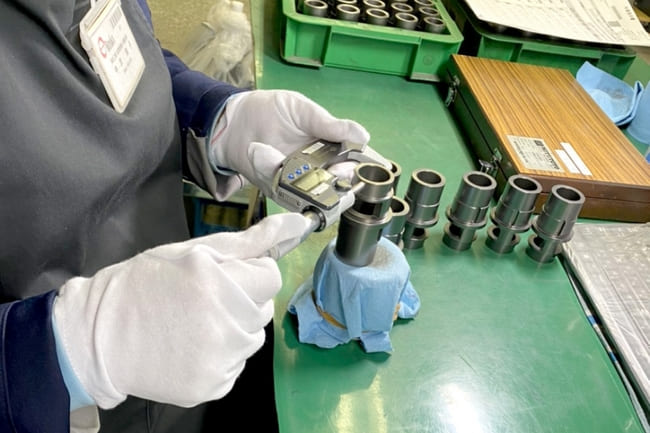
Based on the inspection forms indicated in the work instructions, inspectors from the quality control department, who are under competence control, perform final checks.
In addition to liner measurements such as calipers and microscopes, we also measure complex shapes and geometric tolerances and surface roughness using CMMs, image dimension measuring machines, and shape measuring machines.
Inspection results are all data managed by serial number, and the process capability index(CPK) and results compared to past LOTs are fed back to the shop floor to improve machining accuracy.
We have also established a traceability system that allows us to immediately recall inspection data from an order number or trace back to a material mill sheet, so we can submit the information at any time.
ISO Effort
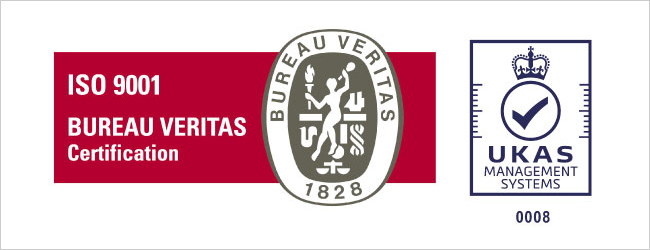
Quality policy
With the goal of enhanced quality in our manufacturing factories and those of subcontracting companies, we will mutually cooperate in thorough investigations of any problem. For communication, we will provide simple and clear communication as we seek enhanced quality.
Furthermore, we will give priority to product innovation (promotion of technical innovation for enhanced productivity) and cost reduction (for enhanced quality) to ensure customer satisfaction through the manufacture of High performance products, and we will abide by the following action guidelines.
Guidelines for action
- By placing priority on quality and trust, we will work to improve quality every day, not only in our company, but also with our subcontracted companies.
- Compliance with laws and regulations.
- We will improve quality by setting the final goals of zero complaints and zero defects both in-house and in our subcontracting companies.
- Gathering the technology and techniques of all employees, we will respond to customer trust with the highest level of quality.
Eco Action 21 Registration
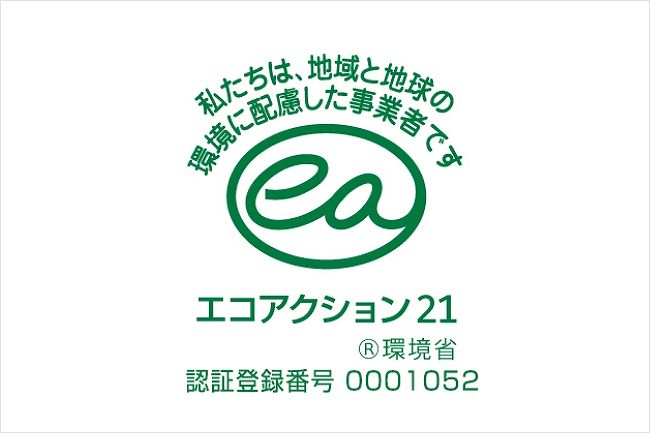
Environmental policy
Environmental idea
IIZUKA & CO., LTD. will continually improve the environmental management system by constructing, operating, and maintaining an optimal system, as well as harmonize corporate activities with nature and recognize environmental concerns as one of the metal product manufacturing factories.
Action policy
- We will abide by environmental laws, local ordinances, and other regulations and preserve the environment to the extent possible.
-
We will strive to optimize the consumption of resources and energy (reduce carbon dioxide emissions).
Reduce power consumption
Reduce fossil fuel consumption (fuel oil, gasoline) -
We will reduce industrial waste and reuse resources.
Thorough separation of general and industrial waste
Enhanced recycling rates - We will strive to optimize the quantity of water resource consumption.
Reduce water consumption - We will promote the transition to eco-friendly goods (green procurement)
For the achievement of this environmental policy, we will notify all employees through environmental education and the necessary training.
Environmental Reports
SDGs Efforts
We support the Sustainable Development Goals (SDGs).
We provide manufacturing services that satisfy our customers with our founding philosophy of “manufacturing that contributes to the next generation of society”.
We could contribute to the realization of a sustainable society, as set forth in the SDGs, by promoting efforts to realize our management philosophy of striving for manufacturing that can contribute to the future of JAPAN through such technologies.
Environment, Social, Safety, and Quality are positioned as the four priority areas. The relationship with the SDGs is as follows.
01 Environment Contribute to reduction of environmental impact through manufacturing.
Environmental Policy
Environmental Idea
Iizuka & Co., Ltd., will continually improve the environmental management system by constructing, operating, and maintaining an optimal system, as well as harmonize corporate activities with nature and recognize environmental concerns as one of the metal product manufacturing factories.
Action Policy
- We will abide by environmental laws, local ordinances, and other regulations and preserve the environment to the extent possible.
-
We will strive to optimize the consumption of resources and energy (reduce carbon dioxide emissions).
Reduce power consumption
Reduce fossil fuel consumption (fuel oil, gasoline) -
We will reduce industrial waste and reuse resources.
Thorough separation of general and industrial waste
Enhanced recycling rates - We will strive to optimize the quantity of water resource consumption.
Reduce water consumption - Promotion of living activities in consideration of environmental activities
- We will promote the transition to eco-friendly goods (green procurement)
For the achievement of this environmental policy, we will notify all employees through environmental education and the necessary training.
2020.May.1
IIZUKA & CO., LTD.
Representative director Hajime Iizuka
We IIZUKA &CO., LTD. is committed to continuous improvement by establishing, operating and maintaining an environmental management system that is aware of environmental issues and in harmony with nature as a manufacturing facility of metal products. We are committed to the sustainable development of our company by recognizing that coexistence with the Earth is a common concern for all humankind, and by making environmental preservation a top priority in all aspects of our business activities.
We are working on environmental issues.
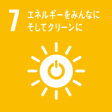
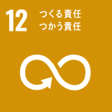
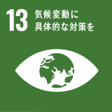
02 Social We want to continue to be a company that is needed by society.
Standards of conduct in stakeholder relations
In conducting business activities, We respect the position of all stakeholders, including customers, subcontractors, society, and employees, and strives for coexistence and co-prosperity with stakeholders while maintaining dignity as trusted company
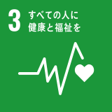
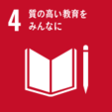
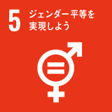
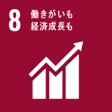
03 Safety Combining safety and productivity
With the goal of contributing to society and the economy through our corporate activities, we always aim to achieve a higher level of safety in all our business activities in order to create a safe and comfortable environment in the global community.
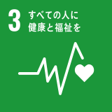
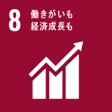
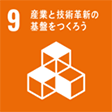
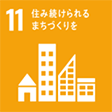
04 Quality Quality is the basis of all our corporate activities.
Quality Policy
With the goal of enhanced quality in our manufacturing factories and those of subcontracting companies, we will mutually cooperate in thorough investigations of any problem. For communication, we will provide simple and clear communication as we seek enhanced quality.
Furthermore, we will give priority to product innovation (promotion of technical innovation for enhanced productivity) and cost reduction (for enhanced quality) to ensure customer satisfaction through the manufacture of High performance products, and we will abide by the following action guidelines.
Guidelines for Action
- By placing priority on quality and trust, we will work to improve quality every day, not only in our company, but also with our subcontracted companies.
- Compliance with laws and regulations.
-
We will improve quality by setting the final goals of zero complaints and zero defects both in-house and in our subcontracting companies.
Quality improvement target
① On time delivery rate
- Inventory reservation order 100%
- Made-to-order products: 85% or more
- Assemble order 100%
- Responded on-time delivery 90% or more
② Cooperative companies compliance rate- Foreign cooperative companies 70% or more
- Domestic cooperative companies compliance rate 70% or more
③ Quality claim 70% or more④ In house defect rate 0.15% or less⑤ Cooperative companies defective rate 0.65% or less -
We respond to our customer’s trust with the highest quality by combining the skills and techniques of all our employees.
2021 Customer satisfaction score 18.5 out of 20.
2021.May.1
IIZUKA & CO., LTD.
Representative director Hajime Iizuka
In order to secure the technology to produce the quality that Iizuka & CO., LTD. aim for, we will build a system in which all employees think, work, and continue to take on challenges.
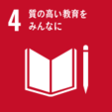
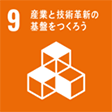
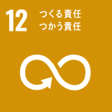
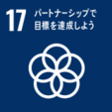