飯塚鉄工所の
技術力・提案力とは
流体機器部品製造で積み重ねた技術と新しい要素を組み合わせるアイデア、「やってみる」という考えを大切に一人一人が小さな改善を具現化することの蓄積がお客様への提案力へとつながります。
生産技術
切削・板金技術の融合による一元化や軽量化のご提案、溶接レスなどの工数削減・製作時のエネルギー削減や鋳造→鍛造の仕様変更、耐食性をもたせるための二層系ステンレス材料提案などコスト・品質・環境を含めた技術提案をパートナー企業とともに実現します。
01ロボットによる作業自動化
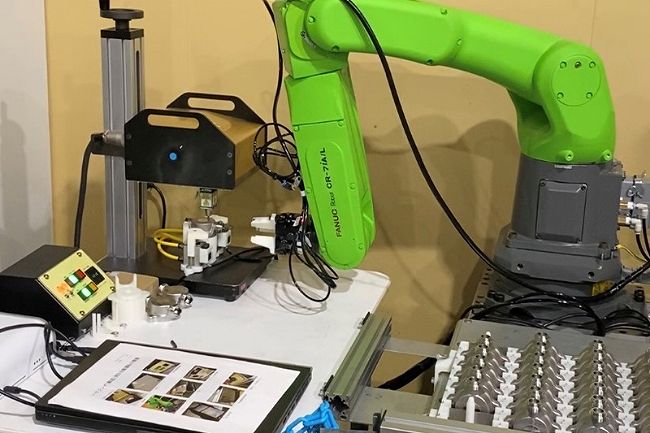
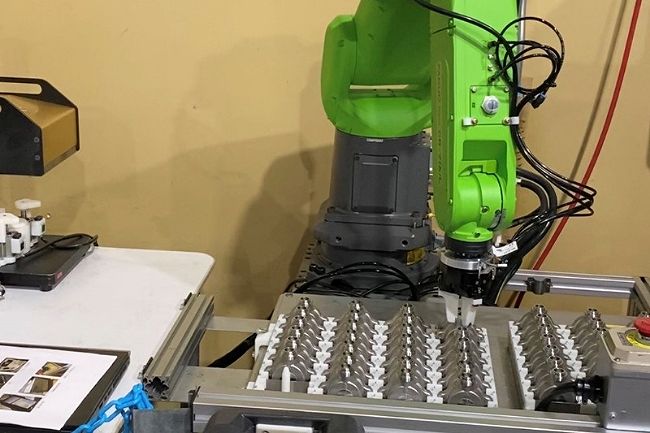
20年前から自動生産に力を入れ、お客様の利益の追求からメーカーに頼らず自社でロボット省人力化システム開発を実現。
増産対応など柔軟な生産体制を構築し、自動化で生み出された製品も多く、お客様からは価格・納期の面でもご満足いただけるようになりました。
02様々な部品のカスタマイズできる受注アプリケーション
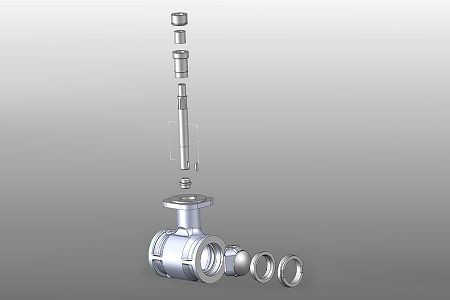
流体機器のオーダーメイドOEM製造(バルブ)
使用する流体性質、使用する環境として圧力、温度に応じて、材質や加工方法をお客様のオーダーに応じて当社で部品製作やアセンブリの対応を行います。
数10点で構成される機能部品の材質や加工方法を1点1点オーダーメイドで様々な組み合わせを基に管理が確立され、部品の製作から部品の品質、在庫、引当管理、キット化から総組立、耐圧検査、非破壊検査まで対応できます。
納期についてはお客様との部品在庫の引き取りの契約をしますと約1か月で出荷ができます。
03デジタル化・見える化ツールの開発
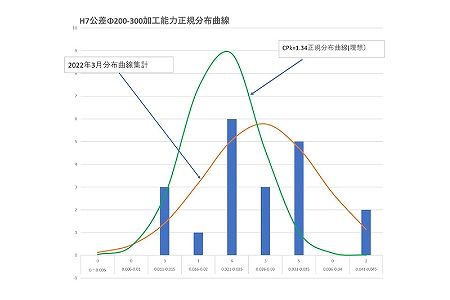
P-FMEA、工程能力管理、公差平均値を出してCPK1.33を目指す
P-FMEAは特定のプロセスの潜在的な障害を操作レベルで分析するのに役立ちます。
当社のデジタル化と見える化のツールを用いて視覚的にわかるような方法を取り入れていくことで現場サイドで目指す位置を明確にしていきます。
また、社内実習室で製品の実際の動きを見る、組立・分解、座学を行い、製品の重要箇所を理解し、品質向上へと役立てています。
技術力
飯塚鉄工所の技術力は、汎用とハイテクの融合です。
従来からの汎用技術はもちろんのこと、その中から生まれる発想の転換をハイテク技術に融合させ、時代の一歩先を行く技術発展に取り組んでいます。
素材においても、素形材・鋳物鍛造からのご提案に加工技術をプラスして融合させます。
01複合加工機を改造し6軸複合加工機を開発
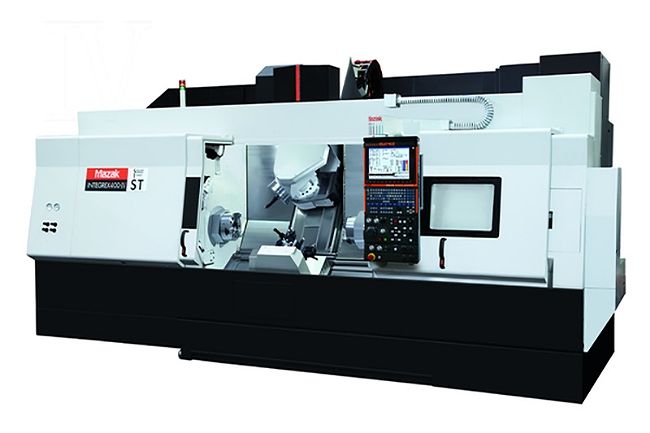
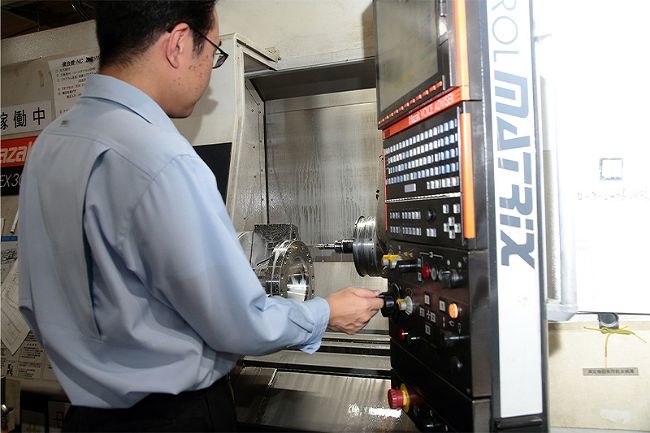
大型マシニングのみの加工であると150時間かかっていた加工を、サーボモーターを付けて角度を変えて加工すればよいのでは?
という発想の転換からA軸をプラスした複合加工機に改造。
様々な角度からの旋盤加工が行うことができ、さらに自社でプログラミング作成できる技術力により、加工時間を15時間に時間短縮を実現。
02東北大学との共同研究でスクリューローターの加工技術特許を取得
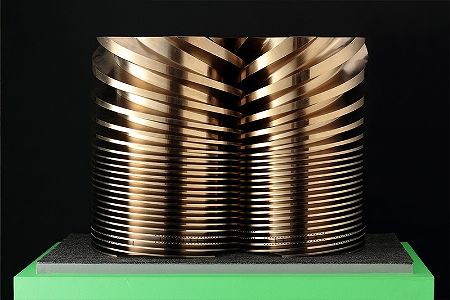
高精度の不等リードスクリュー製造技術を確立し、加工時間を従来の10分の1へ短縮することに成功。
特許も取得。不等リードスクリューは半導体や太陽電池などの製造における生産性の向上や省エネ化・低コスト化に貢献することを可能とした排気能力の高い新型真空ポンプの心臓部品です。
03最新のベンダー機及びレーザー加工機とパンチプレス機の複合機を導入
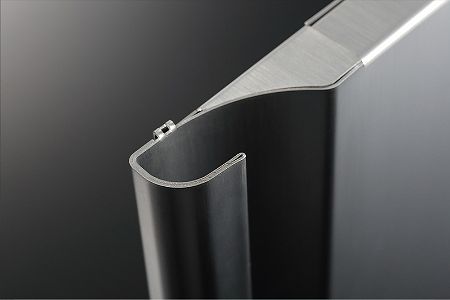
ベンダー機は試作・多品種少量生産にてお客様に総合的メリットを出すことができ、レーザーパンチ複合機では高速レーザー切断だけでなくフォーミング加工も可能とし、生産コストだけでなく工程間のコスト削減をお客様にご提案致します。
特に設計段階より携わらせて頂く事で新技術の提案・新しい発想により、更にコストを抑えた製品製作をさせて頂きます。
今まで諦めていたもの、出来なかったものにもチャレンジしますので是非ご相談下さい。
04専門的な知識、技術を習得させる人財育成
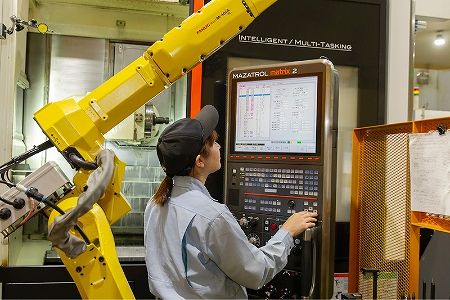
最新技術を身に付けたいという意欲のある従業員の活気に満ちあふれています。
良い人財の育成も技術力の一つと考えております。
年数を重ねるごとにさらなるレベルアップに向けて専門的な知識の必要な資格なども取得可能で、教育体制についても全面的に支援しています。
資格取得実績 | 合格者 |
---|---|
技能検定 機械加工(数値制御旋盤作業)1級 | 2名 |
技能検定 機械加工(数値制御旋盤作業)2級 | 6名 |
技能検定 機械加工(マシニングセンタ作業)1級 | 2名 |
技能検定 機械加工(マシニングセンタ作業)1級 | 3名 |
技能検定 機械検査(機械検査作業)2級 | 2名 |
非破壊試験技術者資格(浸透深傷試験)レベル2 | 1名 |
非破壊試験査技術者資格(浸透深傷試験)レベル1 | 3名 |
職業訓練指導員 | 2名 |
ステンレス鋼溶接技能者(TN-FV) | 2名 |
VA / VE提案
ものづくりを通してお客様の声をキャッチし、分析・アイデア・チームワークによりコストダウンにとどまらない品質の向上、生産の効率化など相互利益のある提案を積極的に行います。軽量化や部品点数削減などさまざまな提案実績があります。
※お客様との守秘義務契約があるため、加工事例を詳細に掲載する事ができません。
実例012017年実用化 ポンプメーカーと共同開発実用化
農薬噴霧器に搭載されるポンプの軽量化・小型化、コストダウンを実現。
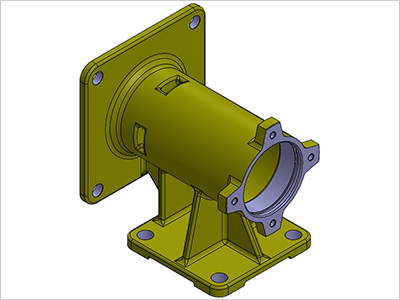
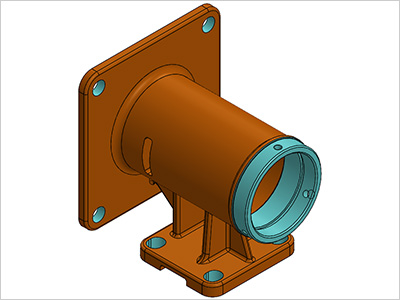
- 【重量】
- 3.2kg→2.7kg 約14%削減
- 【サイズ】
- 全長144mm→全長132mm 約10%小型化
実例022019年実用化 半導体製造装置メーカーと共同開発実用化
チラー(液体温度調節装置)に搭載される製品のロストワックス化による部品点数の削減。
各部品製作+溶接で製作していたものをロストワックス+溶接へ変更を行い、部品点数の削減と溶接工数を削減。
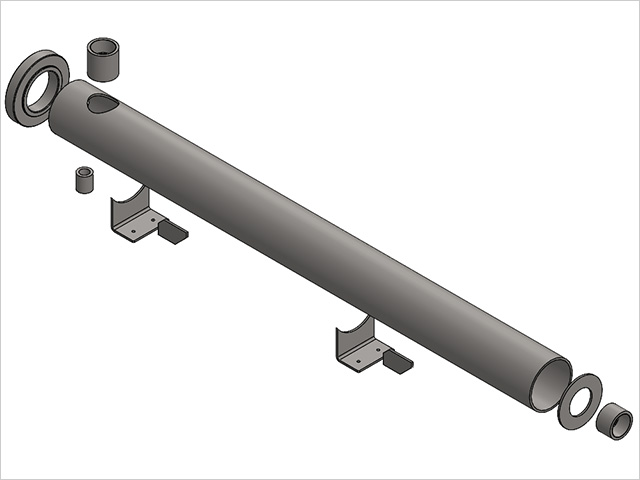
部品点数:10点
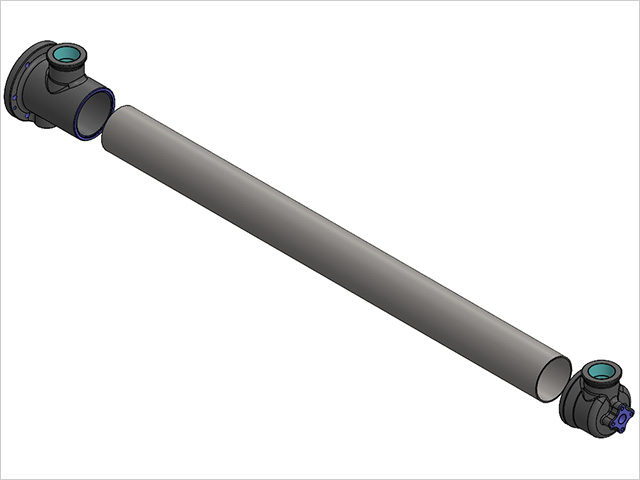
部品点数:3点
実例03バルブメーカーへ回転構造部品点数の削減提案事例
現行のメーカー製品はハンドルの回転機構の動きが円滑ではないことが課題。
この問題を解消するには構造と加工の制限から高価となるのが懸念事項。
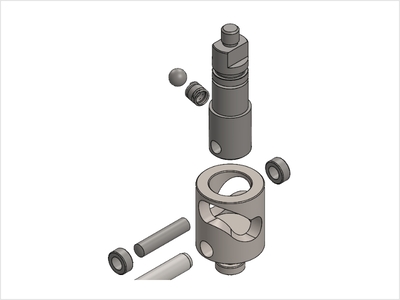
従来品
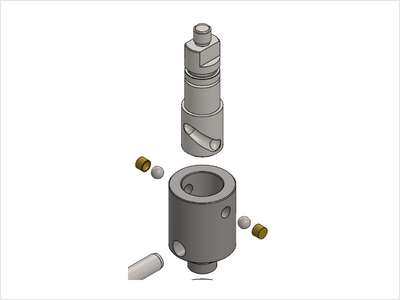
生技開発品
当社生産技術部にて構造の簡素化、加工の容易化を計り、回転機構の円滑化と部品点数の削減によるコストダウンを提案。